Is Yellow Zinc Conductive
Yellow zinc basically is not conductive. But in the presence of moisture, it can conduct a little bit of electricity.
Zinc is an excellent conductor of electricity in and of itself. However, when chromate is mixed with zinc for zinc coating, it increases surface resistance. As a result, zinc’s conductivity decreases.
Yellow zinc plating or zinc coating is another form of corrosion-resistant zinc plating or coating. As a result, yellow zinc cannot be categorized as an electrical conductor.
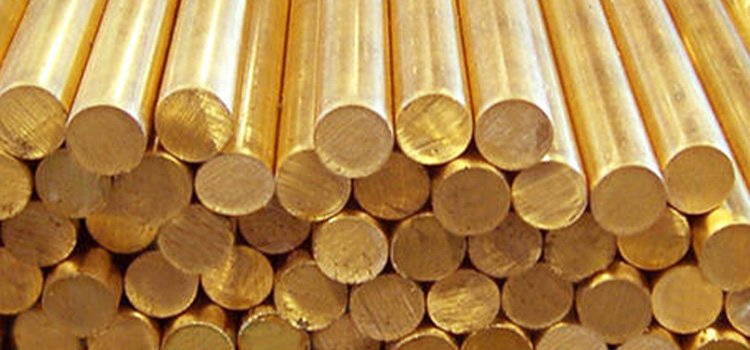
Is Yellow Zinc Conductive
The coating offers corrosion protection for regions of exposed steel surfaces, such as cutting edges and places where the coating has been damaged, due to the sacrificial nature of the zinc.
However, because of the zinc coating, their conductivity falls when the zinc’s surface resistance rises as a result of the coating.
What Is Yellow Zinc
Yellow zinc is a type of zinc plating that involves applying chromate which has a high trivalent or hexavalent chromium concentration to the surface of an item after it has been zinc plated.
Advantages of Yellow Zinc
- Corrosion resistance is greater than normal zinc or blue zinc
- Cost-effectiveness is better
- Enhanced aesthetic qualities
Yellow Zinc Plating Applications
- Automotive parts
- Consumer products
- Contactors
- Fasteners
- Mechanical components
What’s the Difference Between Clear Zinc and Yellow Zinc
The hue of the chromate utilized on the component’s surface is what the term yellow in the yellow zinc refers to. Yellow chromate inhibits zinc from corroding and improves the finish’s overall protection. This finish has prominent yellow tones and has a rainbow or iridescent effect.
Is Yellow Zinc Better Than Zinc
Normal zinc is beneficial in a variety of applications, and zinc is an essential component of our body’s functioning. And zinc plating, also known as galvanization, is the process of coating a metal component with a thin layer of aluminum to give a protective layer.
Zinc plating is frequently used to give a protective coating against corrosion caused by water and other elements in the air. Zinc coatings are commonly applied to iron and steel because these metals rust rapidly.
Use of Different Zinc Coatings
Zinc coatings come in a variety of forms. These zinc coatings can be used for a variety of purposes. Zinc coatings are divided into three categories. Yellow zinc, black zinc, and blue zinc (sometimes known as transparent zinc) are the three types of zinc.
Yellow zinc is the most often used corrosion-resistant metal for automobile components. The corrosion resistance of black zinc is somewhat lower than that of yellow zinc. The least corrosion-resistant zinc plating is blue or transparent zinc.
How Long Does Yellow Zinc Plating Last
Zinc-plated coatings should not be used in applications that are exposed to the elements. In outdoor settings such as metropolitan coastal regions, zinc-plated bolts and hardware fittings, such as gate hinges, do not provide significant corrosion protection and often do not survive more than 12 months.
Is Yellow Zinc Resistant to Heat
Although zinc electroplating can tolerate temperatures up to 500 degrees Fahrenheit, it cannot resist temperatures over 212 degrees Fahrenheit, since its defensive corrosion ability begins to deteriorate at that point. If the temperature is above 500F, zinc plating should be avoided.
Frequently Asked Questions
Is yellow zinc plating resistant to rust
This iridescent electroplated zinc finish, commonly known as Yellow Zinc Chromate offers excellent corrosion and rust resistance. This finish should not be used in areas where there is a lot of salt spray.
Conclusion
Zinc coatings have the benefit of being extremely corrosion resistant. They also give corrosion resistance. Yellow zinc, on the other hand, is not an excellent conductor in terms of conductivity. Because the transparent zinc coating enhances the surface resistance, the zinc becomes more resistant.
Subscribe to our newsletter
& plug into
the world of circuits